Welcome to DU!
The truly grassroots left-of-center political community where regular people, not algorithms, drive the discussions and set the standards.
Join the community:
Create a free account
Support DU (and get rid of ads!):
Become a Star Member
Latest Breaking News
Editorials & Other Articles
General Discussion
The DU Lounge
All Forums
Issue Forums
Culture Forums
Alliance Forums
Region Forums
Support Forums
Help & Search
Environment & Energy
Related: About this forumAn Additive Manufacturing Process for Producing Polymeric Neutron Shields for Fission and Fusion Nuclear Reactors.
Here's a pretty cool paper I almost overlooked, which involves an interesting approach to neutron shielding. Although personally, I'm opposed to wasting neutrons, there are situations in which they need to be managed, particularly in relatively small nuclear reactors. Thus I found the following paper interesting:
Identifying Syndiotactic Polypropylene as a Promising Candidate for Polymer Laser Powder Bed Fusion and Neutron Shielding Materials Ying Han, Hao Jiang, Xiulian Chen, Jun Liu, Ruiqian Zhang, Shiping Song, and Yijun Li Industrial & Engineering Chemistry Research 2025 64 (7), 3785-3794.
From the introductory text:
Nuclear energy is advancing across the multidimensional fields of “sea, land, air, and space.” Micronuclear power sources can significantly enhance the long-term endurance of aircraft, ships, and satellites, offering important applications. (1) Radiation shielding for nuclear reactors is a core component that protects the structural integrity and integrated electronic systems of specialized reactors from neutron and γ radiation. (2) However, the shielding system for special nuclear power sources differs significantly from the radiation shielding used in land-based reactors, with strict weight and volume constraints. Therefore, it is essential to develop smaller, lighter, and more adaptable shielding solutions for complex, irregular surfaces while meeting stringent shielding requirements. (3)
Neutron radiation is a form of ionizing radiation composed of high-speed neutrons featuring strong penetrating power, (4,5) which allow it to pass through various materials and especially, thermal neutrons with energy range between 0.025–1 keV are most likely to impact human health. (6) Hydrogen-rich polymers and their composites, incorporating elements with high neutron absorption cross sections such as boron (B) and cadmium (Cd), can effectively moderate and absorb neutrons and are frequently used as front-end shielding materials for effective neutron shielding. However, the increasing complexity of neutron shielding device structures, driven by the development of microreactor nuclear power sources, demands manufacturing processes that can efficiently adapt to irregular surface geometries. Unfortunately, the traditional processing techniques like compression molding and injection molding suitable for polyethylene, (7,8) epoxy resins, (9) high-temperature resistant polyimides, (10) flexible rubbers, (11) and hydrogen-rich benzoxazines (HRB), (12) are limited to producing conventional plate-shaped components and lack the capability to fabricate products with complex geometries or special shapes. This significantly restricts the flexibility and design adaptability of shielding parts, making it difficult to effectively wrap protective components for nuclear radiation shielding.
Polymer laser powder bed fusion (PBF-LB/P), a highly representative additive manufacturing technology, (13) can precisely and rapidly produce complex structures to meet the protection needs of irregular geometries in microreactor nuclear power sources. However, the primary sintering materials in the PBF-LB/P domain are semicrystalline long-chain polyamides (PA), (14,15) such as polyamide 6 (PA6), polyamide 12 (PA12), and their composites, as well as thermoplastic polyurethane (TPU). Due to their high cost and significant postcondensation phenomena, polyamide powders are not suitable as base materials for large-scale neutron shielding device production. Polypropylene (PP), one of the most cost-effective general-purpose plastics, offers advantages such as low density, low processing temperature, and good chemical resistance. The high hydrogen content in PP molecules enhances its neutron moderation efficiency. However, research on the application of PP in the PBF-LB/P field has been limited, primarily due to the high melting temperature (Tm > 165 °C) of isotactic polypropylene (iPP) and its rapid crystallization rate and high crystallinity, which lead to warping and printing failures during the sintering process, or significant deviations in part accuracy due to postcondensation. Very recently, syndiotactic polypropylene (sPP), with a different spatial configuration from iPP, has –CH3 groups alternately arranged on both sides of the molecular chain, resulting in greater flexibility and enhanced resistance to thermal degradation. (16,17)...
...Based on the crystallization behavior of syndiotactic polypropylene (sPP), this study successfully achieved the PBF-LB/P processing of sPP powder for the first time and applied it to neutron radiation shielding, addressing three key objectives: (1) revealing the isothermal and nonisothermal crystallization behavior of sPP to verify its processability in PBF-LB/P; (2) determining the optimal printing parameters for sPP in PBF-LB/P processing to ensure low shrinkage and dimensional stability; and (3) evaluating the neutron shielding performance of sPP and its products. (24−26) This study not only expands the range of materials suitable for PBF-LB/P but also provides new insights into enhancing the processing methods for complex and precise polypropylene structures...
Neutron radiation is a form of ionizing radiation composed of high-speed neutrons featuring strong penetrating power, (4,5) which allow it to pass through various materials and especially, thermal neutrons with energy range between 0.025–1 keV are most likely to impact human health. (6) Hydrogen-rich polymers and their composites, incorporating elements with high neutron absorption cross sections such as boron (B) and cadmium (Cd), can effectively moderate and absorb neutrons and are frequently used as front-end shielding materials for effective neutron shielding. However, the increasing complexity of neutron shielding device structures, driven by the development of microreactor nuclear power sources, demands manufacturing processes that can efficiently adapt to irregular surface geometries. Unfortunately, the traditional processing techniques like compression molding and injection molding suitable for polyethylene, (7,8) epoxy resins, (9) high-temperature resistant polyimides, (10) flexible rubbers, (11) and hydrogen-rich benzoxazines (HRB), (12) are limited to producing conventional plate-shaped components and lack the capability to fabricate products with complex geometries or special shapes. This significantly restricts the flexibility and design adaptability of shielding parts, making it difficult to effectively wrap protective components for nuclear radiation shielding.
Polymer laser powder bed fusion (PBF-LB/P), a highly representative additive manufacturing technology, (13) can precisely and rapidly produce complex structures to meet the protection needs of irregular geometries in microreactor nuclear power sources. However, the primary sintering materials in the PBF-LB/P domain are semicrystalline long-chain polyamides (PA), (14,15) such as polyamide 6 (PA6), polyamide 12 (PA12), and their composites, as well as thermoplastic polyurethane (TPU). Due to their high cost and significant postcondensation phenomena, polyamide powders are not suitable as base materials for large-scale neutron shielding device production. Polypropylene (PP), one of the most cost-effective general-purpose plastics, offers advantages such as low density, low processing temperature, and good chemical resistance. The high hydrogen content in PP molecules enhances its neutron moderation efficiency. However, research on the application of PP in the PBF-LB/P field has been limited, primarily due to the high melting temperature (Tm > 165 °C) of isotactic polypropylene (iPP) and its rapid crystallization rate and high crystallinity, which lead to warping and printing failures during the sintering process, or significant deviations in part accuracy due to postcondensation. Very recently, syndiotactic polypropylene (sPP), with a different spatial configuration from iPP, has –CH3 groups alternately arranged on both sides of the molecular chain, resulting in greater flexibility and enhanced resistance to thermal degradation. (16,17)...
...Based on the crystallization behavior of syndiotactic polypropylene (sPP), this study successfully achieved the PBF-LB/P processing of sPP powder for the first time and applied it to neutron radiation shielding, addressing three key objectives: (1) revealing the isothermal and nonisothermal crystallization behavior of sPP to verify its processability in PBF-LB/P; (2) determining the optimal printing parameters for sPP in PBF-LB/P processing to ensure low shrinkage and dimensional stability; and (3) evaluating the neutron shielding performance of sPP and its products. (24−26) This study not only expands the range of materials suitable for PBF-LB/P but also provides new insights into enhancing the processing methods for complex and precise polypropylene structures...
An interesting graphic, a graphic reflecting combinatorial optimization, from the paper:
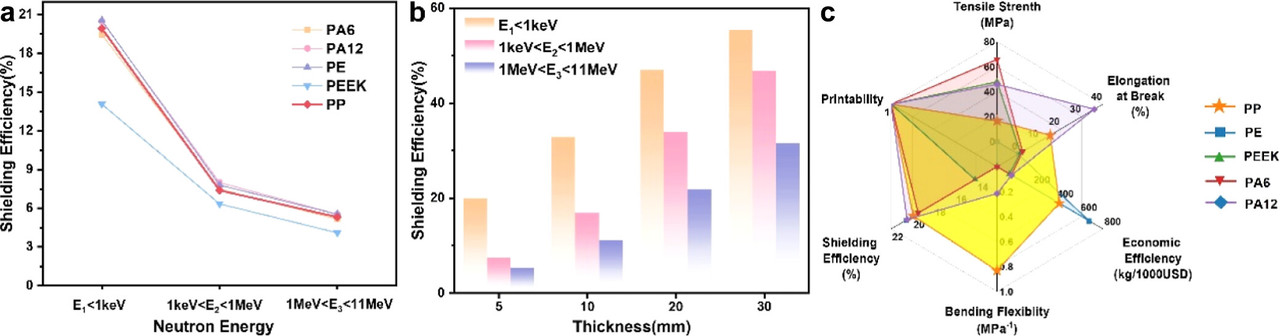
The caption:
Figure 5. (a) Neutron shielding efficiency of various materials across different energy ranges. (b) Neutron shielding efficiency of sPP with different thicknesses across different energy ranges. (c) Performance comparison of sPP and other polymers.
My son is seeking his Ph.D. in a field involving additive manufacturing, although his work involves 3D printing of metals as opposed to the more widely applied 3D printing of polymers. I'll share this paper with him.
I trust you're having a pleasant Sunday in spite of the impending collapse of our country by suicide.